Partnership with LambWeston / Meijer vof
Lamb Weston / Meijer vof
Kruiningen, The Netherlands
1991 - present
Capacity: 5,000 m3/d.
Anaerobic UASB treatment: 5,000 m³
Biogas production: 6,000,000 million Nm3/year
Biogas treatment: 3.500 ppm to <10 ppm
Nitrogen removal: 1,750 kg per day ; 96% removal
Phosphate recovery: 2,000 tonnes per year
Colsen started providing consultancy services to LambWeston in Kruiningen in 1991, due to continuing problems with water treatment. As it happened, the anaerobic water treatment system was not working properly, because it would be disrupted after every weekend. Colsen analysed the system, the pollution load, the various side-streams and the water used for cleaning during the weekend cleaning process. This analysis showed that the work carried out in the weekend would disrupt the water treatment process due by discharging fat and lye into the water. On top of that, the influent of the aerobic treatment system contained a lot of sand and clay from the washing department. Colsen and LambWeston tackled and solved these problems together, and after this introduction, Colsen was involved in all plans to expand production and the resulting consequences for the sewerage and water treatment systems. Separate fat and starch sewerage systems were set up, and the pyrophosphate and blancher approach was substituted with a sprayer system installed on the dryers. Steps were also taken towards improved sludge processing by building a sludge thickener.
Permits & infrastructure
Colsen was also involved in preparing applications for discharge permits and Environmental Management Act permits. From a combined advisory role, Colsen often played a part in setting up infrastructure, building parking lots and roads, as well as renewing large parts of the pressure discharge system leading to the Westerschelde.
Colsen also oversaw several soil remediation and soil protection processes.
Master plan
A water-treatment master plan was designed in order to keep up with continuous increases in production, which saw Colsen and LambWeston partner up in a construction team to realise the following components:
- Organising the regional storage and disposal of tare soil;
- In the past, all sewage sludge was still wet when it was transported to farmers, We managed to reduce the amount of sludge transported with a thickening process, before introducing mechanical sludge dewatering with centrifuges.
- Washing water treatment in sedimentation ponds and an aeration/buffer pond;
- Washing water treatment and pumping systems in the washing department with effluent reuse;
- Wastewater pre-sedimentation by converting the post-sedimentation system into a pre-sedimentation system;
- Gray starch dewatering system and storage silos;
- Expansion of the anaerobic water treatment system by building several anaerobic reactors fed by a central mixing tank;
- Steam boiler conversion to run on biogas. Followed by the installation of a CHP system and biogas desulphurisation system. Later on, this biogas treatment system was replaced by a Colsen biogas treatment system. (BIDOX®);
- Development and realisation of a new more environmentally friendly phosphate removal system (ANPHOS®). This system removes phosphate from anaerobically pre-treated water thanks to struvite-based phosphate recovery.
- Expansion of the aerobic water treatment system by replacing basins with concrete tanks with bubble aeration in a nitrification/denitrification system;
- Expansion with two new sedimentation tanks;
- Modification and conversion of the aerobic treatment system into an improved nitrogen removal system (NAS®).
Result
Originally, the underlying goal of the water treatment system was to meet discharge requirements for treated wastewater. Over the years, however, the water treatment system became a source of renewable energy, water and resources. Thanks to the continuous improvements in anaerobic water treatment technology, LambWeston managed to produce more and consume less energy, aided by improvements made in the aeration process. With the introduction of the new nitrogen removal process (NAS®), the amount of energy required for aeration was reduced by 50%, as was the production of sewage sludge. Phosphate is now recovered by means of struvite production, which can be put to good use as a fertiliser and helps cut the operating costs of phosphate removal.
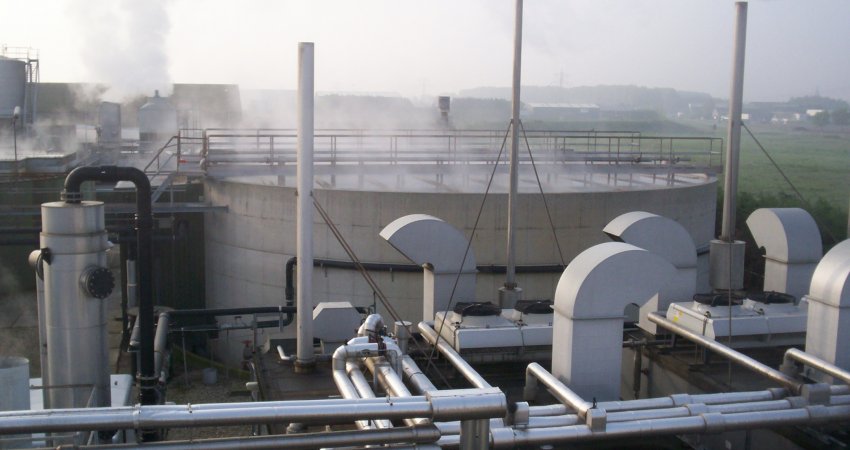
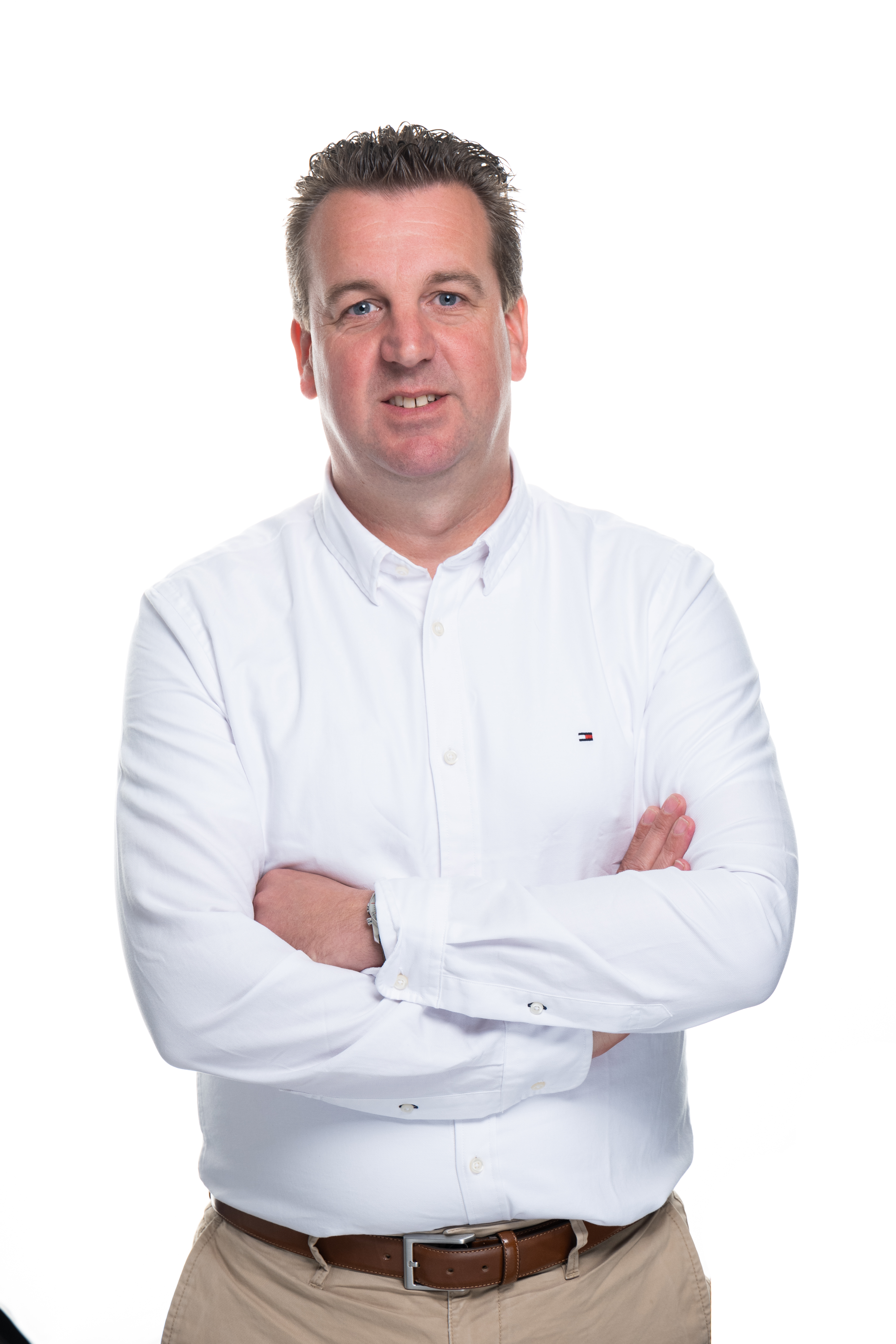
Would you like to know more?
Ask
Boris
Boris Colsen, Managing Director